Effective Inventory Management for Business Success
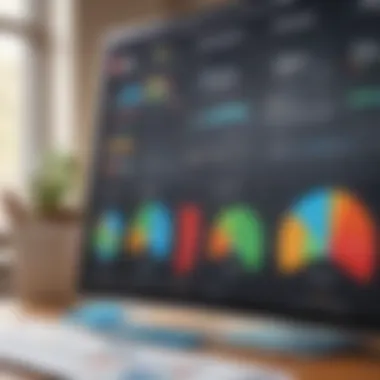
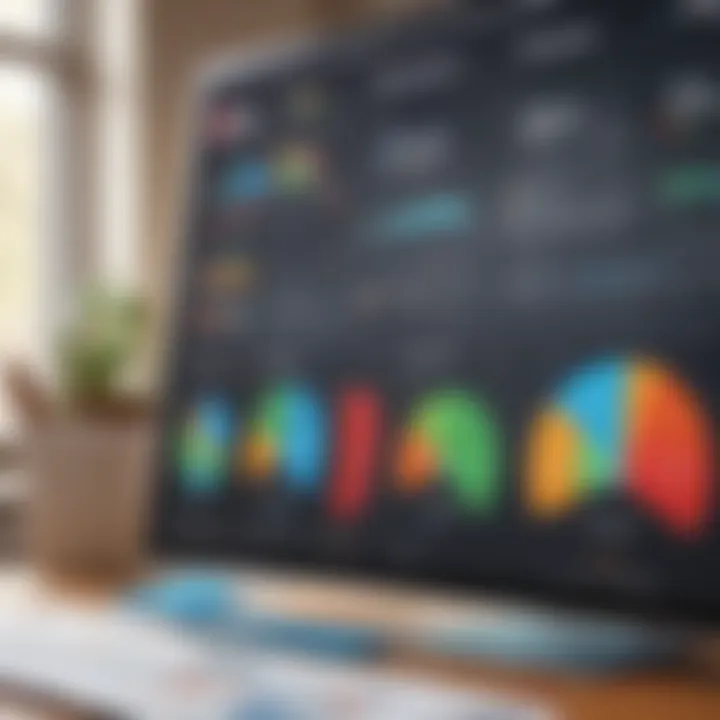
Intro
When it comes to running a business, successful inventory management can make or break your operational efficiency and profitability. Think of inventory as the beating heart of any organization; if it's functioning well, the whole body thrives. Conversely, a poorly managed inventory can lead to stagnation or even complete failure. Understanding how to weave inventory management seamlessly into your business plan is not just a choice; itâs a necessity.
Consider how various industries tackle inventory differently. A tech startup might focus on just-in-time inventory systems to keep overheads low, while a retail giant likely relies on bulk purchasing strategies to negotiate lower costs. Each method has its merits and can significantly impact your bottom line, customer satisfaction, and overall business agility.
In this article, weâll dig deep into integrating inventory management into your broader business strategy. We'll explore key terms, discuss best practices, and shed light on the tools available that can elevate your inventory management game from mediocre to exceptional. Let's embark on this journey to understand why inventory management is the unsung hero of many successful companies.
Understanding Inventory in Business
Inventory plays a pivotal role in the successful operation of any business. It's not just a bunch of products or materials piled up in a warehouse; it's a strategic element that can either propel your business forward or hinder its growth. To understand inventory in a business context, one must consider what it representsâan investment, a resource, and a critical factor in customer satisfaction. Knowing how to effectively manage inventory can lead to improved operations, cost savings, and heightened customer loyalty.
Definition of Inventory
Inventory can be defined as the stock of goods or materials that businesses hold. This includes raw materials, work-in-progress items, and finished products, all crucial to fulfilling customer demands. It's important to recognize that inventory isn't merely a buffer against demand fluctuations; it also serves as a tangible representation of a company's operational strategy. A clear understanding of inventory helps in shaping not only the logistics and supply chain but also its financial health.
Types of Inventory
Raw Materials
Raw materials are the essential inputs required to create a product. Think of them as the very building blocks of manufacturing. Their contribution to the overall production process can't be overstated. A well-managed inventory of raw materials ensures that production runs smoothly without interruption. One key characteristic of raw materials is their direct correlation to production costs; managing these effectively can lead to significant savings. An additional aspect to consider: raw materials can be volatile in price, creating challenges for businesses without solid tracking systems in place.
Work-in-Progress
Work-in-progress (WIP) inventory comprises items that are in the manufacturing process but aren't yet complete. It plays a significant role in balancing supply with continuous production flow. The vital characteristic of WIP is its potential impact on cash flow; excessive WIP can lock up capital that could otherwise be used more effectively. However, WIP allows companies to maintain a steady output, helping to meet customer demand without delays, which is often a beneficial aspect for businesses that operate on just-in-time production systems.
Finished Goods
Finished goods are the end products ready for sale to customers. They represent the culmination of the entire production process. A key feature of finished goods is their direct relationship with customer satisfaction; if a company has the right products in stock, it can meet consumer demand quickly. However, excess finished goods can also mean overstocking, which ties up cash and incurs additional holding costs. Balancing the right amount of finished goods inventory is crucial for financial health and operational efficiency.
Maintenance, Repair, and Operations Supplies
Maintenance, Repair, and Operations (MRO) supplies include items necessary for the upkeep of a company's operations but not directly involved in production. These supplies are often overlooked yet are vital for minimizing downtime and ensuring operational efficiency. One of the unique features of MRO supplies is their unpredictable nature; unlike finished goods, their necessity can arise unexpectedly. However, effective management of MRO supplies can significantly reduce operational disruptions and maintain workflow continuity.
Importance of Inventory Management
The significance of inventory management cannot be overstated. It integrates various aspects of a business, from operational efficiency to financial management, directly impacting customer satisfaction. Developing a comprehensive inventory management strategy enables businesses to streamline their operations and optimize resources.
Operational Efficiency
Operational efficiency is about maximizing output while minimizing waste. Efficient inventory management contributes directly to this goal by ensuring that materials and products are available as needed. One characteristic that stands out here is timing; having the right inventory levels can significantly reduce lead times and enhance service delivery. This is especially crucial in industries where time is of the essence, like retail and e-commerce.
Cost Management
Effective cost management in inventory involves tracking the various costs related to stockâeverything from storage to spoilage. One remarkable element of this is the concept of carrying costs, which entails all expenses tied up in holding inventory, including warehousing, insurance, and depreciation. By effectively managing these costs, a business can enhance its profit margins, ensuring that funds are allocated efficiently, rather than wasted.
Customer Satisfaction
Customer satisfaction hinges heavily on product availability and timely delivery. A strong inventory management strategy ensures that businesses can meet customer expectations consistently. The key aspect of this is understanding demand fluctuations; knowing when to ramp up stock levels or when to cut back can prevent stockouts or overstock scenarios, both of which can harm customer trust and satisfaction.
Efficient inventory management not only influences financial performance but is also integral in shaping customer relationships.
To wrap it up, understanding inventory in business goes beyond just holding stock. It's about crafting a strategic approach that considers various inventory types, management practices, and the ultimate goal of serving customers efficiently while keeping costs in check.
Incorporating Inventory Strategy into Business Planning
In today's dynamic business landscape, integrating an inventory strategy within the overall business plan is not just an option; it's a necessity. The approach to inventory management can significantly shape operational efficiency, drive customer satisfaction, and ultimately enhance profit margins. When inventory decisions align with broader business objectives, companies can respond quickly to market demands, avoid stockouts, and ensure that resources are utilized effectively. A well-planned inventory strategy allows businesses to keep a close eye on trends, manage risks, and adapt to changing circumstances.
Linking Inventory to Business Objectives
Linking inventory management to business objectives means aligning stock levels and inventory turnover with the company's strategic goals. For instance, if a company aims to penetrate a new market, having the right products in the right quantities is crucial. This alignment enables businesses to capitalize on opportunities and mitigate potential pitfalls. By keeping inventory levels in sync with objectives, companies can optimize cash flow and enhance responsiveness to customer needs.
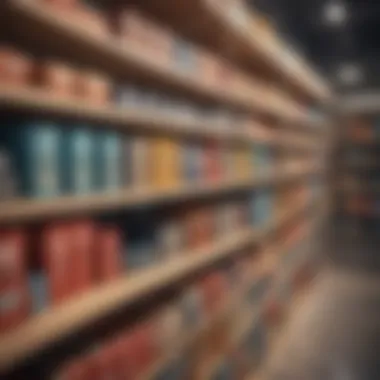
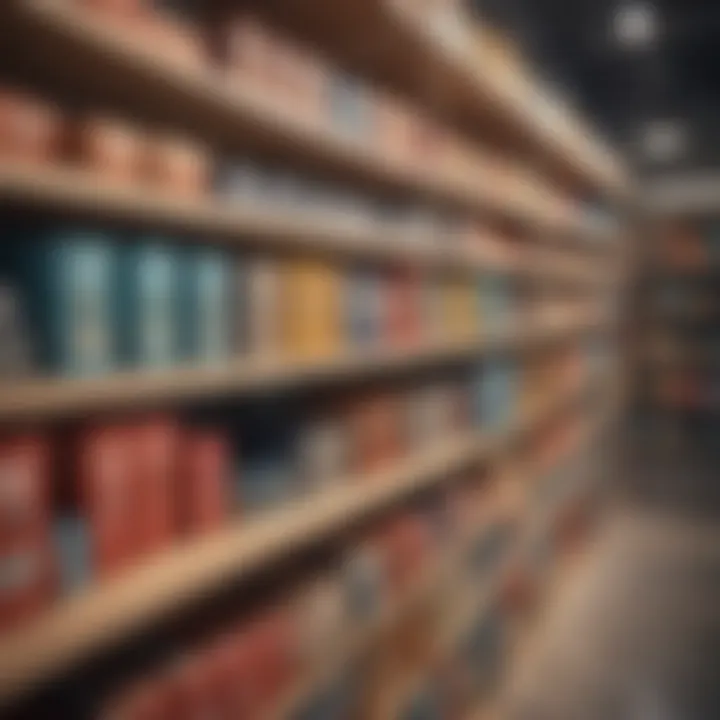
Assessing Inventory Needs
Understanding how to assess inventory needs is vital for ensuring that a business can meet demand without overstocking or understocking. This assessment is twofold, encompassing market demand analysis and sales forecasts.
Market Demand Analysis
Market demand analysis dives deep into consumer behavior and market trends. By studying patterns in purchasing, companies can gauge what products are likely to be popular at any given time. This analysis is particularly useful for seasonal items, where demand fluctuates dramatically during certain periods. A key characteristic of market demand analysis is that it leverages real-time data, helping businesses make informed decisions. The unique feature of this analysis lies in its predictive capability, which can be a game-changer for businesses looking to stay ahead in a competitive market. However, it also has its challenges, as relying solely on past data may not fully capture emerging trends.
Sales Forecasts
Sales forecasts offer a structured way to estimate future sales, directly impacting inventory decisions. By considering historical sales data, marketing plans, and economic indicators, companies can create informed projections. The benefit of using sales forecasts is the ability to anticipate demand spikes or dips, allowing businesses to adjust their inventory accordingly. One of the unique features of sales forecasts is their adaptability; they can be adjusted as new information emerges. However, the reliability of forecasts can be hindered by unforeseen market shifts or changes in consumer sentiment.
Inventory Cost Considerations
Managing inventory is not just about stock levels; it's equally about understanding the costs associated with it. Various factors contribute to the total cost of inventory, including storage costs, capital expenditure, and insurance and write-offs.
Storage Costs
Storage costs encompass all expenses related to holding inventory. This includes warehouse rents, utilities, and labor associated with maintaining inventory. By keeping these costs minimized, businesses can significantly enhance profitability. A major advantage of understanding storage costs is that it encourages businesses to evaluate their warehousing choices. However, reduced storage costs shouldnât compromise the quality of inventory management since inadequate facilities might lead to damaged goods.
Capital Expenditure
Capital expenditure refers to the funds used by a business to acquire or upgrade physical assets like buildings and equipment. In the context of inventory, companies need to balance the capital tied up in stock with their financial flexibility. One of the key characteristics of capital expenditure is its long-term impact on a business, influencing everything from cash flow to investment opportunities. If not managed wisely, capital tied up in excess inventory can hinder growth.
Insurance and Write-Offs
Insurance and write-offs are crucial for protecting a business's assets. Insurance costs cover potential losses due to theft, damage, or obsolescence while write-offs account for unsellable inventory. Itâs essential for companies to factor in these aspects when planning inventory. The significant characteristic of this consideration lies in its risk management potential. Companies that implement robust strategies can limit financial exposure and take informed risks. However, itâs crucial to note that excessive write-offs can signal deeper issues within inventory management, potentially highlighting inefficiencies that need addressing.
"A seamless integration of inventory strategy within a business plan is not merely beneficial; It's essential for survival in a competitive marketplace."
Incorporating an inventory strategy into the overall business planning not only ensures alignment with objectives but also enhances the organizationâs capability to adapt to market conditions. It acts as the backbone for sound decision-making and sustainable growth.
Techniques for Effective Inventory Management
Inventory management is not just about keeping track of goods; itâs a strategic approach influencing a company's entire operation. By employing specific techniques, businesses can greatly improve their efficiency, reduce waste, and ultimately enhance customer satisfaction. These techniques facilitate better decision-making by aligning inventory levels with customer demand, thus safeguarding against overstocking and stockouts. In an era where responsiveness to market changes is crucial, these techniques provide the agility needed to navigate complexities in supply chain management.
Just-In-Time Inventory
Just-In-Time (JIT) is a powerful methodology aimed at reducing flow times within production systems as well as response times from suppliers and customers. This technique is designed to ensure products are produced or delivered only as they are needed, minimizing storage costs and reducing potential waste. The core attribute of JIT is its emphasis on timing, which resonates particularly well in sectors where customer preferences shift rapidly.
Adopting JIT can yield notable benefits, primarily through cost savings and operational efficiency, but it does bring along challenges such as the necessity for precise forecasting and reliable suppliers. When executed correctly, JIT enables businesses to maintain lean inventories, thus freeing up capital for other uses.
ABC Analysis
ABC Analysis serves as a valuable method for categorizing inventory based on their importance to overall sales and business objectives. This technique divides inventory into three segments: A, B, and C, facilitating prioritization in managing different stock items.
Categorizing Products
The heart of ABC Analysis lies in Categorizing Products. This classification identifies which items require the most attention and resources, helping streamline efforts across the board. For instance, 'A' items are the most valuable, typically representing a small percentage of total inventory but a large portion of overall value. Conversely, 'C' items are less critical, often accounting for a larger volume but lower value.
This categorization is beneficial because it allows managers to allocate their time and investment more effectively, focusing on key items that make a significant impact on profit and operational success. However, it necessitates periodic reviews for maintaining accuracy in categorization to adapt to changing market dynamics.
Prioritizing Management Efforts
Prioritizing Management Efforts hinges on the key principle that not all inventory items should be treated equally. By understanding which items are crucial to the revenue stream, businesses can focus their resources where they matter most. This aspect of ABC Analysis goes a step further by emphasizing that you get more bang for your buck when you devote management efforts to those high-impact items.
A unique feature of prioritization is its capacity to optimize inventory turnover, but it can also pose a risk. Over-focusing on 'A' items might lead to neglect of 'B' and 'C' goods, potentially disrupting the supply chain balance or creating unwanted stockouts in lower-priority areas. Therefore, a delicate balance must be maintained.
Inventory Turnover Ratios
Inventory Turnover Ratios serve as a key metric for assessing how well a company manages its inventory.
Calculation Methods
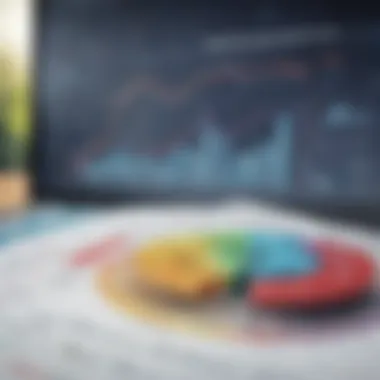
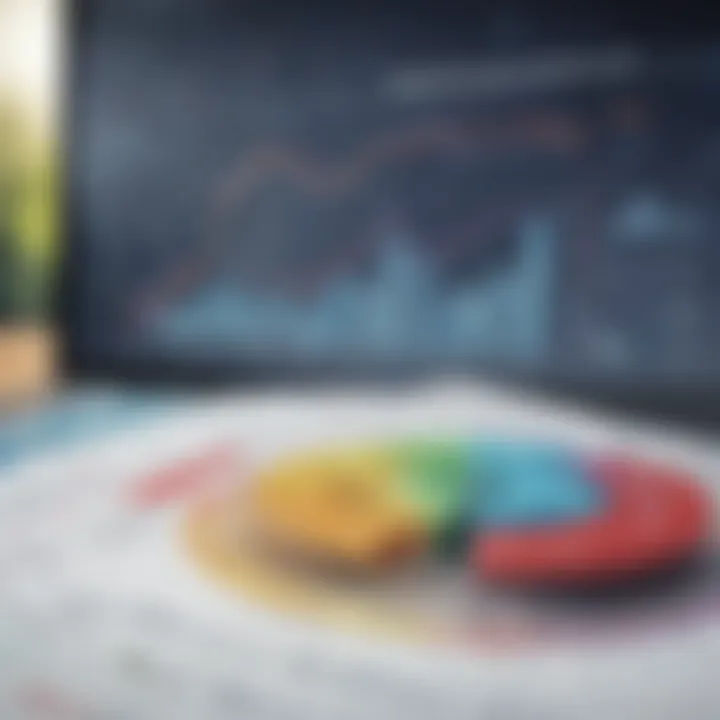
To gauge efficiency in inventory management, understanding Calculation Methods for turnover ratios is essential. This calculation generally involves dividing the cost of goods sold (COGS) by the average inventory during the same period. The simplicity of this formula is advantageous as it functions effectively across various industries. A higher turnover ratio typically indicates good sales and effective inventory management, keeping products flowing through the business without unnecessary hoarding.
On the flip side, an overly high ratio might suggest insufficient stock levels, risking lost sales opportunities. Hence, striking an optimal turnover ratio is crucial for maintaining a smooth operational flow.
Interpreting Results
Once turnover ratios are calculated, understanding how to interpret results is vital for inventory strategy. The key characteristic of interpreting results involves recognizing that no single number is a definitive measure of performance. Instead, context mattersâsuch as historical performance and industry benchmarks.
Interpreting results can illuminate trends, flagging if shifts in turnover ratios indicate broader issues like mismatched demand forecasts or changing customer preferences. A thoughtful analysis can uncover insights that lead to proactive adjustments in inventory strategies, ensuring that businesses remain aligned with market dynamics.
Tools and Technology in Inventory Management
In the age of digital transformation, integrating the right tools and technology in inventory management is no longer optional; it's a necessity. These elements not only streamline operations but also ensure that businesses maintain an edge in a competitive landscape. With advancements in inventory management software and automation, businesses can handle their stock levels with laser precision, reducing waste and improving service delivery.
Technology, in this context, acts like a compass, guiding decision-making and promoting strategic alignment with overall business objectives.
Inventory Management Software
To make informed decisions, understanding inventory management software is crucial. This software encompasses systems designed to track inventory levels, orders, sales, and deliveries. These systems serve as a foundation on which effective inventory management is built.
Features to Consider
When evaluating inventory management software, several features should not be overlooked. Real-time tracking is key; it allows for immediate visibility into stock figures. If a store is running low on a particular item, the software can alert staff automatically, enabling quick reordering.
Another valuable characteristic is integration capabilities. A good software should work seamlessly with existing systemsâthink accounting software or e-commerce platformsâto create a holistic approach to inventory management. This integration not only saves time but also minimizes the risk of errors during data transfer.
Those unique features afford businesses the agility needed to adapt quickly to changes in demand or supply chain disruptions, thus improving overall operational efficiency.
Cost-Benefit Analysis
Engaging in a thorough cost-benefit analysis before choosing an inventory management solution is paramount. For businesses, this means weighing the expense of purchasing and implementing the software against the potential savings and efficiency improvements it can bring.
A key factor to consider is return on investment (ROI). Outstanding software may require a higher upfront cost, but if it significantly reduces carrying costs or stockouts, it can yield considerable financial benefits in the long run. Vendor support and training are another aspect; good software comes with training to help staff navigate the system, thus ensuring smooth operations.
The main challenge here is to assess the long-term value against immediate costs, as a less expensive solution might not meet performance expectations, leading to more expenses down the line.
Automation in Inventory Processes
Automation represents another layer of innovation that enhances inventory management. By minimizing manual intervention, organizations can streamline processes, reduce errors, and free staff to undertake more strategic tasks.
Benefits of Automation
The benefits of automation are multi-faced. For starters, it fosters efficiency, allowing tasks such as order processing and inventory tracking to run smoothly without human error. Additionally, automated systems often come equipped with data analytics, offering detailed insights and forecasts that inform decision-making.
An enticing feature of automation is scalability. As a business grows, an automated system can adapt without significant changes to the underlying infrastructure. This adaptability ensures that as demand rises, supply chain processes can match it without a hitch.
Challenges to Implementation
However, diving headfirst into automation is not without its challenges. Implementation can throw a curveball at companies, particularly those that havenât used sophisticated systems before. Training needs may arise, requiring a dedicated team to facilitate a smooth transition. Also, there's the risk of becoming too reliant on technology, which could pose problems if systems fail.
Companies must also think about initial costs. Automating inventory processes typically comes with notable expenses, which can deter businesses with tight budgets. Striking a balance between investment and payoff becomes vital in evaluating whether to implement automated solutions.
"In todayâs fast-paced market, not leveraging technology is almost akin to walking a tightrope without a net."
In essence, the integration of tools and technology in inventory management is not merely supplementary; it is essential for operational management that aligns with business goals. By making thoughtful choices about inventory management software and automation processes, businesses can significantly enhance their operational resilience and customer service delivery.
Monitoring and Evaluating Inventory Performance
Monitoring and evaluating inventory performance is an essential cog in the wheel of effective business management. It allows organizations to maintain a pulse on how well they manage stock and helps identify areas needing improvement. With performance evaluation, businesses can ensure they are not just meeting demand but also doing so efficiently, enabling profitable operations. The act of oversight here isnât just about keeping tabs on stock; itâs also about using data to inform better decisions moving forward.
Key Performance Indicators
Key Performance Indicators (KPIs) serve as vital signs for your inventory system. Letâs delve into some specific indicators that ring a bell in virtually every business setting.
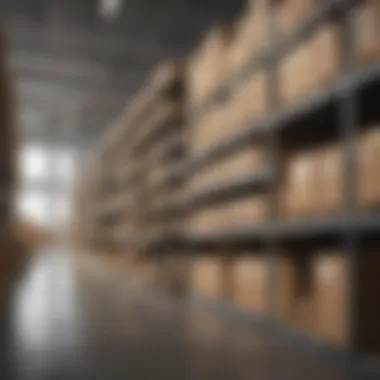
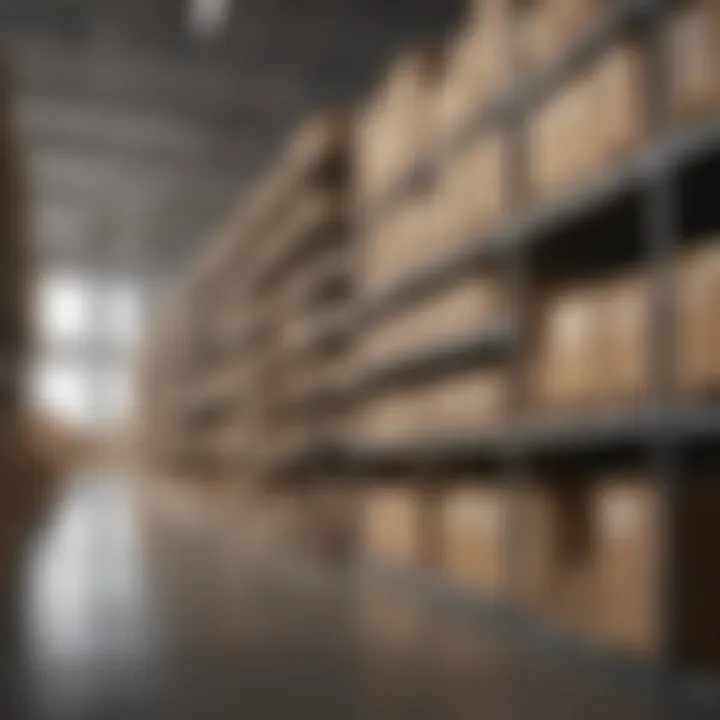
Inventory Accuracy
Inventory accuracy closely measures how well the recorded stock levels match the actual stock. This aspect is crucial because poor accuracy can lead to either overstocking or stockouts, both of which drain resources and customer goodwill. One of the standout characteristics of inventory accuracy lies in its ability to boost efficiency. With precise records, staff can easily find what they need without wasting time. One big plus is that it supports better financial planningâknowing exactly what's on your shelves helps create more accurate budgets.
"Inventory accuracy reduces operational headaches and improves service delivery."
However, achieving accuracy isnât all sunshine. It requires robust systems and methods for regular checks, which can be resource-intensive. Moreover, reliance solely on technology can sometimes lead to blind spots in manual processes.
Stockout Rates
Stockout rates measure how often items go out of stock. This metric is crucial in understanding customer experienceâafter all, losing a sale because a product isnât available can lead a customer to switch to a competitor. A critical characteristic of stockout rates is their ability to highlight inefficiencies in the supply chain. Low stockout rates indicate good inventory forecasting and management, allowing a business to meet customer demand in real-time.
Yet, thereâs a flip side. If stockouts are frequent, this signals that the inventory system isnât aligned with demand, which might require a swift reevaluation of inventory processes or supplier relationships. Static stockout rates donât reveal the full picture but can be a powerful tool when tracked over time to spot patterns.
Carrying Costs
Carrying costs refer to the total expenses associated with holding inventory. This includes everything from warehousing to depreciation, insurance, and taxes. Understanding carrying costs is vital because they can eat away at profit margins if not monitored effectively. A fundamental characteristic of carrying costs lies in revealing inefficienciesâhigh carrying costs can mean a business is either overstocked or failing to utilize its inventory effectively.
Unique feature? Well, assessing carrying costs closely ties into understanding your overall financial health. This metric can drive strategic decisions about purchasing and pricing. But, if poorly managed, it can lead to excessive capital being tied up in unsold goods, which hinders growth.
Regular Audits and Reviews
Having a schedule for regular audits and reviews reinforces the commitment to monitoring inventory performance. These practices are not merely about verifying numbers but about cultivating a culture of diligence and accountability.
Procedures for Inventory Audits
Procedures for inventory audits are systems put in place to ensure that stock records are consistently verified against physical stock. Good procedures not only help catch discrepancies but also streamline the process to reduce downtime during audits. A beneficial choice, indeed, because a structured audit procedure brings clarity and organization.
However, these procedures require constant refinement to cope with changes in inventory dynamics. Rigid procedures may become obsolete, needing periodic updates to remain effective. Still, when done correctly, audits can identify issues that may not be apparent at first glance.
Adjusting Business Plans Based on Findings
Adjusting business plans based on findings from inventory evaluations helps ensure that strategies remain relevant and effective. This dynamic approach allows businesses to pivot when data indicates a shift in customer needs or market trends. A key characteristic of these adjustments is their adaptability; businesses can react swiftly to challenges or opportunities.
While beneficial, these adjustments can sometimes lead to instability if changes are too frequent or not considered thoroughly. Hence, assessing the impact of changes before implementation is crucial to ensure that they align with overall business goals.
In sum, monitoring and evaluating inventory performance isnât just about tracking stock; itâs about integrating insights into the very fabric of business strategy. Keeping an eye on these performance metrics not only safeguards against pitfalls but lays a solid foundation for sustained growth.
Future Trends in Inventory Management
Understanding future trends in inventory management is essential for aligning your business plan with emerging market demands. As the landscape evolves with technological advancements and shifting consumer preferences, businesses must adopt innovative practices to stay competitive. The integration of inventory management into your business plan needs to consider these trends to enhance operational efficiency and mitigate risks.
Impact of E-Commerce
E-commerce has dramatically changed the way businesses manage their inventories. The growth of online shopping necessitates a more agile inventory system capable of supporting increased turnover rates. Businesses need to ensure products are available in real-time to meet consumer demand while balancing cost management strategies. To achieve this, integrating inventory management software with e-commerce platforms can provide data-driven insights.
For example, retailers like Amazon utilize sophisticated algorithms for inventory allocation, allowing them to predict stock requirements based on consumer buying patterns. Consequently, adapting inventory practices to meet e-commerce demands not only increases customer satisfaction but also improves overall profitability.
Sustainability in Inventory Practices
Sustainability has moved to the forefront of business practices, particularly when it comes to inventory management. To be relevant, companies must consider both Environmental Considerations and Efficient Resource Use as part of their strategy.
Environmental Considerations
Thinking green is no longer just a trend; it's a necessity. Minimizing waste through efficient inventory management contributes to a healthier environment. A key characteristic of sustainable practices is the reduction of surplus inventory which, in turn, lessens the environmental footprint.
Moreover, employing methods like lean inventory reduces the risk of obsolescence by avoiding overproduction. As a strategy for sustainability, many businesses are adopting the principles of the circular economy, which emphasizes reusing materials and minimizing waste. This choice is beneficial, as it not only lowers costs but also enhances the brand image among eco-conscious consumers. However, achieving such sustainability requires an upfront investment in training and systems that might take time to show returns.
Efficient Resource Use
Efficient resource usage is another crucial aspect of modern inventory management. This focuses on optimizing existing resources to reduce overall costs and increase productivity. By simplifying processes related to order fulfillment and stock management, businesses can free up resources that can be allocated elsewhere.
For instance, the adoption of just-in-time inventory practices allows companies to maintain minimal stock on hand, which is both a cost-saving and space-efficient strategy. While this model may lead to occasional stockouts, its advantages often outweigh potential downsidesâlike lower inventory holding costs.
These resource-efficient strategies can significantly enhance the overall sustainability levels in a business, creating a competitive edge in a crowded marketplace.
"In the future, businesses that fail to integrate sustainable inventory practices risk falling behind their competitors who prioritize both efficiency and environmental impact."
In summary, the future of inventory management is tied intricately to e-commerce growth and sustainability practices. Companies willing to adapt and innovate in these areas are more likely to succeed, effectively responding to modern consumer demands while promoting a sustainable business model.